Improved uptime with 50% lower water use for separation in vegetable oil production
Vegetable oil processing from soybeans or sunflower seeds is low-margin, bulk production with a clear dependency on maximum uptime and optimized operating expenses. Thanks to the diligent assistance of Alfa Laval’s service people, two major vegetable oil producers in South Korea and Turkey have cut their cooling water requirement by 50 percent and lowered the maintenance costs for their centrifugal separator from Alfa Laval by 80 percent.
DATE 2024-03-21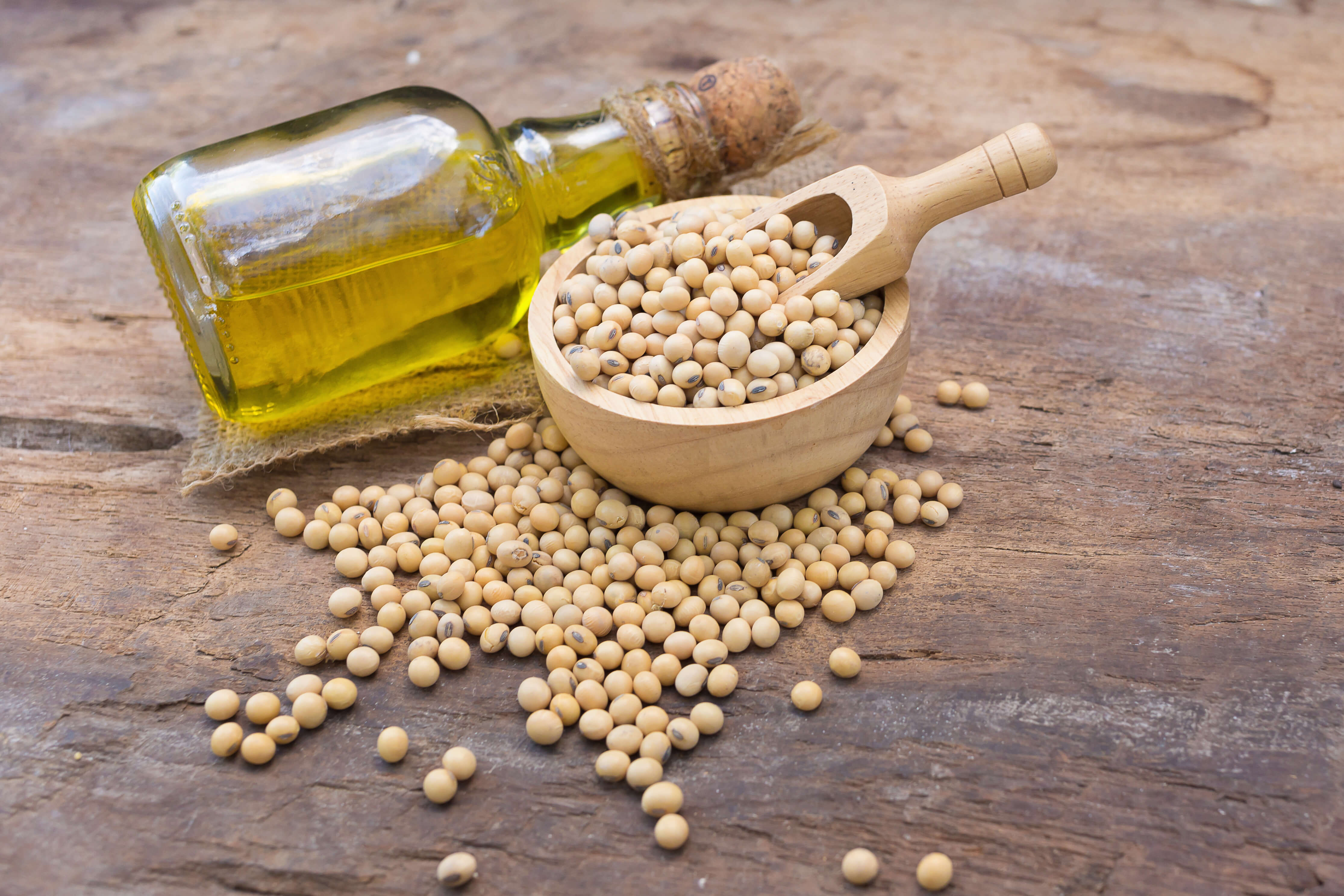
All it took was a simple upgrade that replaced a double-seal inlet with a single-seal inlet. The solution is now recommended wherever the PX separators are used for processing vegetable oils, lard, tallow, and fish oil.
The companies were already satisfied with the performance of the Alfa Laval PX separators installed at both factories. However, both companies had concerns about the high operating and maintenance costs of the separators’ inlet seals.
“The double inlet seal arrangement is only needed if an inert gas system is used or if bowl flushing is required, but it was standard on the PX separators,” explains Baris Bulut from Global Service Sales at Alfa Laval. “For these vegetable oil companies, maintaining the two seals was taking up 70 percent of their standard maintenance budget. This is a heavy burden when you consider that this is not a high-value product. It’s an essential everyday ingredient, and producers need to keep their separators in operation as far as possible 24/7.”
With this feedback very much front of mind, Alfa Laval developed a complete conversion kit for its PX range of industrial centrifugal separators for vegetable oils, lard, tallow, and fish oil.
The conversion can be completed in approximately two hours, transforming the inlet device, which consists of a double inlet seal, into a new inlet device with a single inlet seal. With a single inlet seal, there are fewer moving parts, which results in lower maintenance costs of more than 80 percent. Also, the conversion makes the separator more robust as the single seal is less sensitive to the quality of supplied cooling water. And last, the demand for cooling water is reduced by 50 percent.
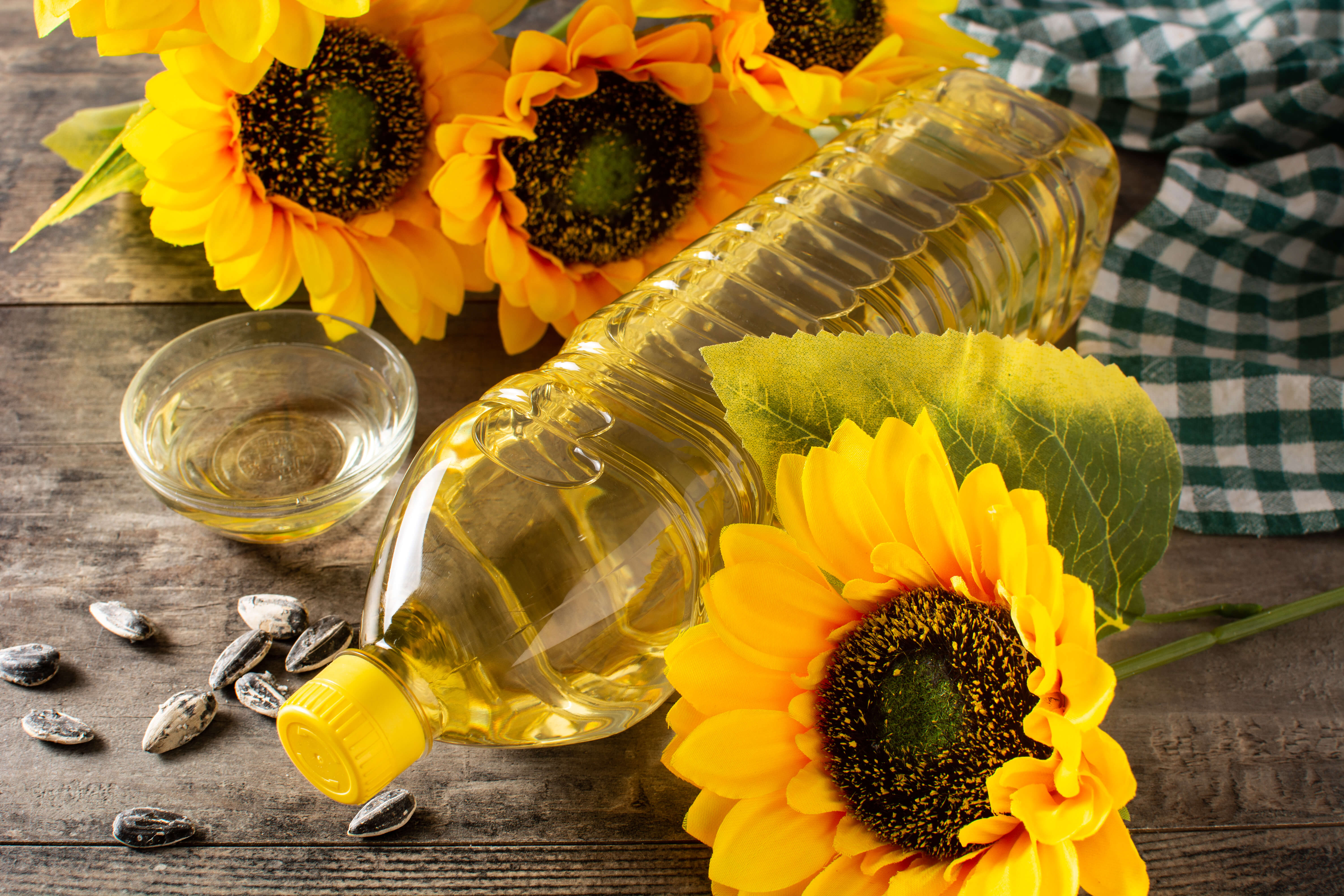
In South Korea, the upgrade enabled the company to better handle the high maintenance costs, particularly high during power outages when the seal water supply failed. Now, the company has reduced costs by three-quarters, and they only need to change a single seal once a year during the annual service. The company has converted two PX80 separators and plans to convert the remaining PX65 to the single inlet seal.
Meanwhile, in Turkey, the conversion has not only lowered maintenance and spare parts costs but also made it easier to keep replacement parts in stock at the factory site.
Since the conversion kit was launched, it has been used to upgrade separators around the world. “It makes sense to upgrade an existing separator when there is sufficient remaining operational lifetime to justify it because the separation performance itself is already superior. This simple and relatively quick upgrade improves sustainability and reliability and reduces operating and maintenance costs,” says Baris Bulut.
Highlighted technologies
Water savings
Reduced cleaning chemical consumption
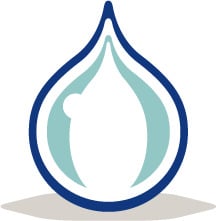
50 percent reduction in the use of cooling water
Cost savings
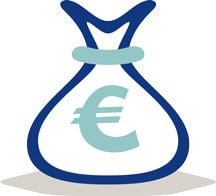
80 percent reduction in maintenance costs
Payback
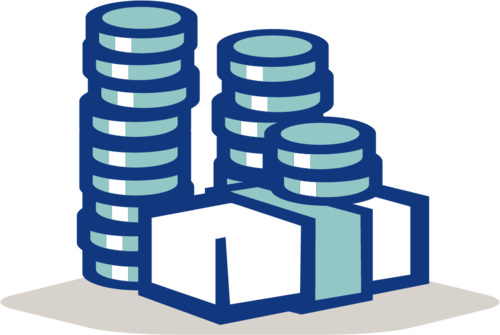
Payback time is between 6-8 months