Perfect pasta: boosting production capacity with Contherm Max
Rising consumer demand for its products highlighted a bottleneck in the production process at Surgital, a prominent Italian food producer. An innovative solution was required to expand capacity and optimize performance. Alfa Laval’s Contherm Max heat exchanger was the answer, and its inclusion in the production process has generated a 20% capacity increase while also cutting €36,000 off the electricity bill and reducing annual CO2 emissions by up to 150 tonnes at the company’s plant in north-east Italy.
DATE 2024-03-07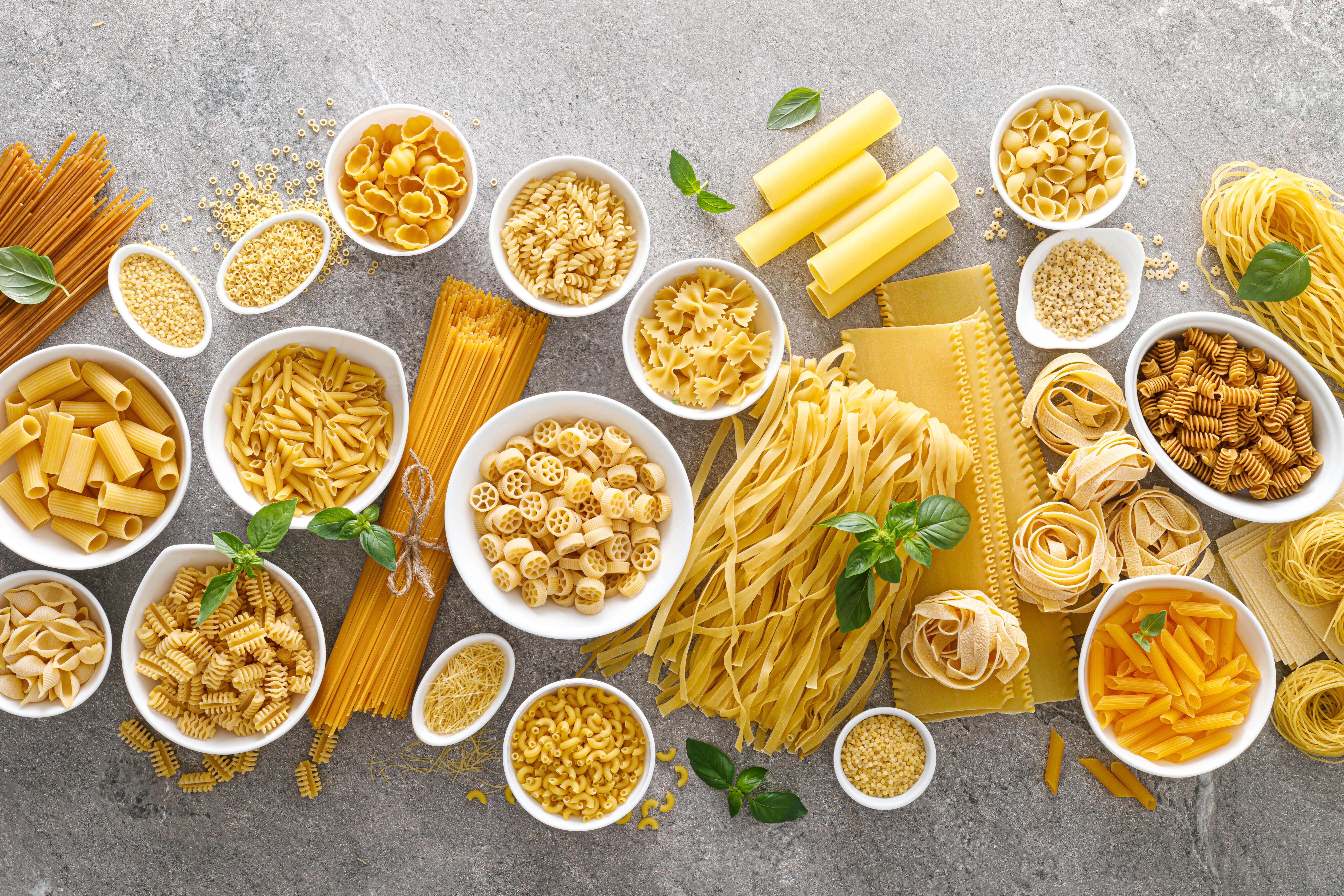
Surgital is Italy’s leading producer of prepared deep-frozen ready meals, pasta and sauces. Established by the Bacchini family in 1980, the company now produces 175 tonnes of fresh pasta, 90,000 single-portion ready meals and 30 tonnes of pasta sauces every day at its production site in Ravenna province.
The popularity and increased demand for these pasta sauces, produced as frozen cubes, revealed a capacity-limiting hold-up in the cooling process. This ultimately led Surgital to call on Tetra Pak and Alfa Laval’s combined process and equipment expertise to expand plant production capability and increase product throughput.
The project team needed to address a problem involving the time taken required to sufficiently cool the sauce to facilitate the cube cutting process.
The original process comprised several steps, starting with tubular heat exchangers, which cooled the sauce from cooking temperature to 45°C. This was followed by two further cooling phases in consecutive air-forced cooling tunnels. The first of these reduced product temperature to -2°C to allow the sauce to be cut into cubes, and the second took the temperature down to -18°C, ready for packaging and dispatch.
The problem lay in the time the product needed to remain in the first cooling tunnel to reach -2°C, which was negatively impacting both the upstream cooking and the downstream freezing processes.
The solution Alfa Laval and Tetra Pak devised was an additional cooling step – installing of a Contherm Max scraped surface heat exchanger to cool the sauce from 45°C to 15°C. This drop in temperature allowed increased throughput in the first cooling tunnel and eliminated the bottleneck.
“The installation of the Contherm Max has enabled Surgital to achieve the goal of capacity expansion and throughput,” says Edoardo Bacchini of Surgital.
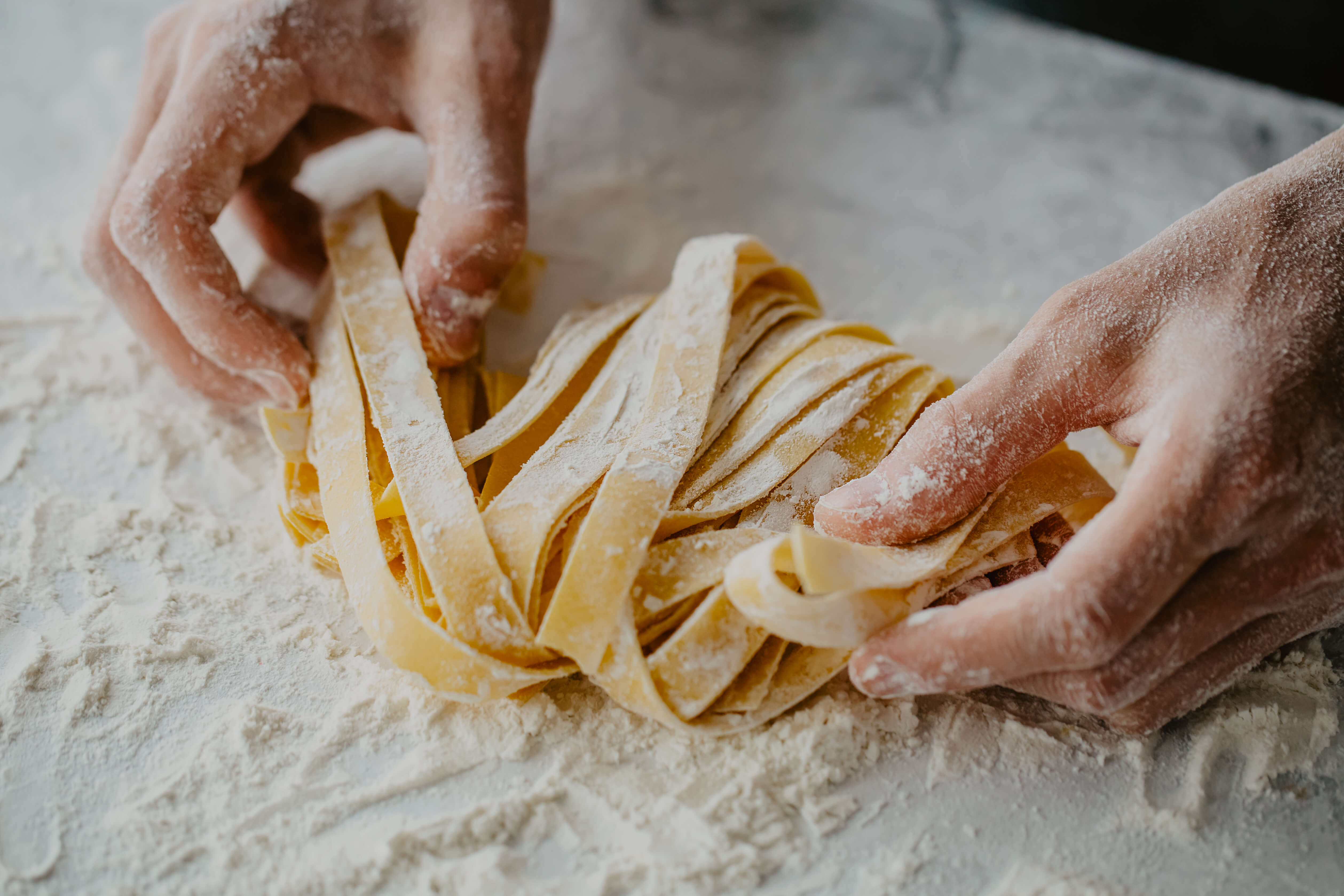
“The proposed solution was significantly more cost-effective than the other options,” says Simone Incerti of Tetra Pak Italy. “The consistent pre-cooling delivered by the Contherm Max has improved the product quality, allowing the production of sauce cubes of a more uniform weight and a more consistent shape among different batches.”
Introducing a scraped surface heat exchanger into the line to perform an efficient precooling of the product enabled Surgital to utilize one of the existing refrigeration systems to obtain the desired capacity increase, explains Giovanni Treglia from Alfa Laval.
“Otherwise, to obtain a comparable capacity increase, the air-forced 1st step cooling tunnel would have had to be expanded, requiring duplication of the current refrigeration system, which would have consumed up to 200 MWh more electricity per year,” he continues. “Thanks to the new Contherm Max, the 1st step cooling tunnel delivers a product temperature that is 3K colder than before, accounting for up to 10 MWh add of electrical energy savings in the downstream freeizing tunnel (2nd cooling step). All in all, the implemented solution is saving €36,000 in electrical energy – equivalent to the annual electricity use in 30 homes – and reducing CO2 emissions by up to 150 tonnes per year.”
Highlighted technologies
Uptime
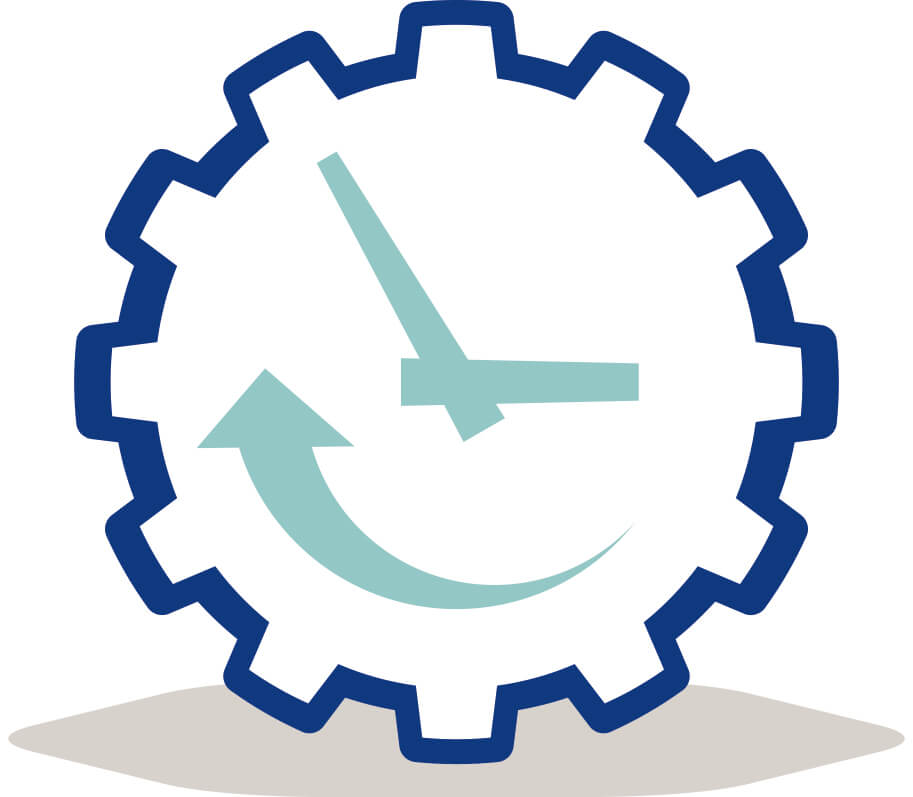
20% capacity increase
Emissions savings
Close to zero carbon emissions in Alfa Laval decanter assembly because all Alfa Laval decanter manufacturing sites run exclusively on sources of renewable energy
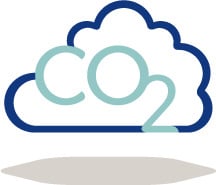
Reducing CO2 emissions by up to 150 tonnes per year
Cost savings
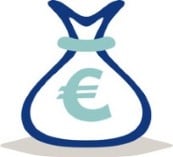
€32,000 reduction in annual maintenance costs
Energy savings
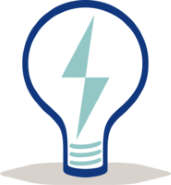
€36,000 in electrical energy savings
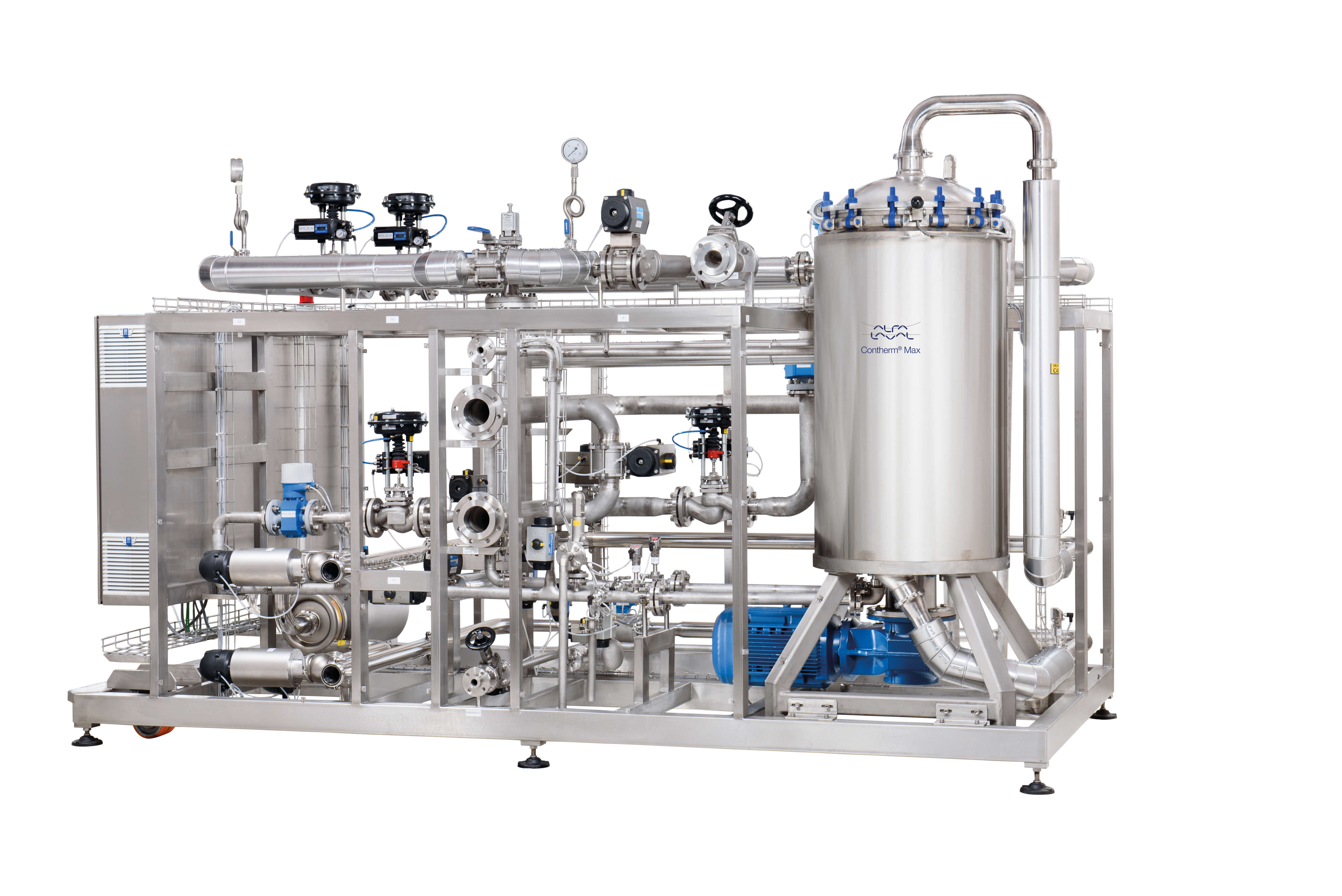
The advantages of this solution were:
• A 20% capacity increase
• Uniform cooling treatment and much colder product temperature at the start of the first cooling tunnel
• Lower product temperature at the tunnel outlet, reaching -5°C and allowing for more precise cube cutting
• Reduced time in the first air-forced cooling tunnel enabling a deeper micro-crystallization of the product and higher quality
• A €32,000 reduction in annual maintenance costs through the inclusion of a twin-screw pump.